If the cotton jersey is to be the visible cover at the neck, tuck the excess jersey inside the neck of the bust form and replace the wooden finial (neck cap) supplied by the manufacturer. Alternatively, a fabric cover can be made by cutting a disc of acid-free card to the size of the neck opening and covering it tightly with cotton jersey (see figure 6.31 and 6.32). The edge of the disc is then neatly slipstitched to the jersey around the neck edge of the form.
A T-shirt can also be used to cover the wadding under the garment. It should fit very tightly and be scoured before use as for a base cover for a mannequin. This works well for later twentieth-century women’s daywear and menswear. It should only cover the wadding and not be visible.
For fragile garments, fine silk habotai8 can be used as a final top cover. Its smooth surface will enable a garment to slide on more easily. It may be necessary to add darts or shaped seams to create a tight fit around the torso. Alternatively, cutting the silk on the bias can work well for a dress where the bust profile is softer and flatter. In this case it is easier to stitch the silk directly to the wadding rather than machine stitch it first (see figure 6.33). Silk habotai also makes a good final cover for arms (sleeve supports, see Chapter 8), especially for garments with tight sleeves, again helping them to slide more easily inside the garment. An inexpensive lightweight silk habotai is ideal for this purpose.
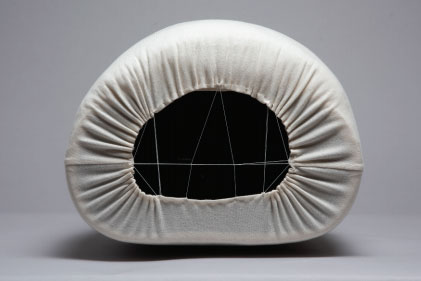
Figure 6.30 Securing the jersey cover under the bottom of the bust form. © Author.
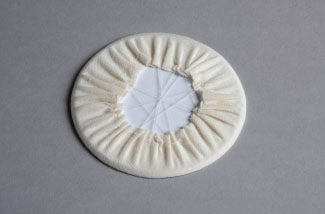
Figure 6.31 Card neck cap covered with cotton jersey. © Author.
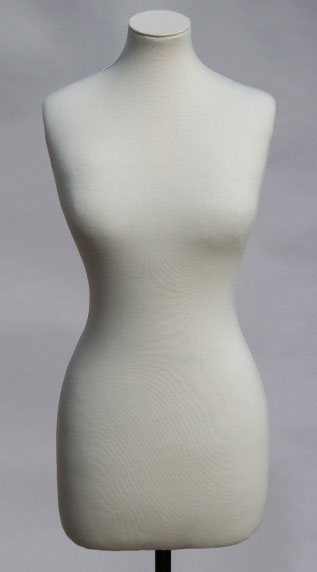
Figure 6.32 Completed stand with fabric neck cover and finished hem. © Author.
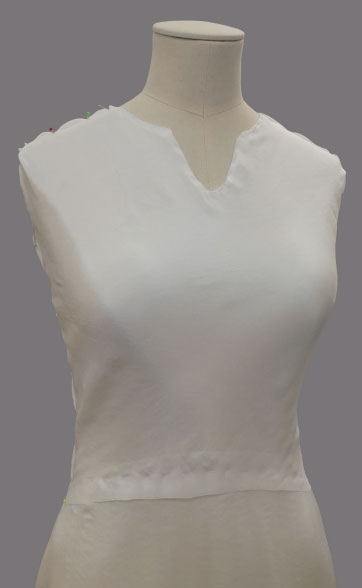
Figure 6.33 Silk top cover hand stitched directly over wadding on the mannequin. © Author.
When trying on a garment over wadding, always cover the wadding with a barrier layer of smooth fabric to prevent the inside of the garment from catching in the wadding fibres. This is particularly important if the bodice is unlined and has loose seam allowances or boning inside. The temporary cover should be light and pliable. Lightweight silk habotai works well as it is soft, slippery and does not add bulk under the garment.
Another option is to use a readymade microfibre slip or petticoat. Vintage nylon or polyester satin petticoats, which can be found in charity shops, can be made into very good temporary covers for trying on garments (see figure 6.34). Whatever method you use always scour the cover to remove any finishing products that might have been added during the production process before trying on garments.
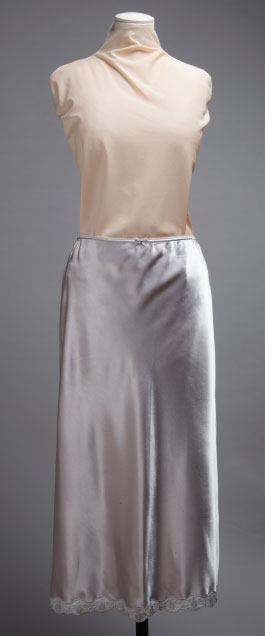
Figure 6.34 1980s polyester satin petticoats made into temporary covers for wadding during fitting trials. © Author.
Summary
The secret to achieving a successful padded form is always having an accurate set of measurements taken from the garment to be displayed. Measuring accurately takes time but once perfected will greatly reduce the number of fittings needed to check whether a garment will fit the display form you have created.
Having taken the measurements, believe in them and do not be tempted to try on a garment if its measurements are smaller than the display form. You will only waste your time and cause additional stress to the garment. The measurements of the form should always be smaller than the garment measurements.
Recording measurements on a measurement chart and using a padding diagram gives an immediate reference of where a particular measurement has been taken and can save time by reducing the need to keep re-measuring.
With a good set of measurements, it is possible to add the basic layers of wadding to a bust form or mannequin without even trying on the garment, thus reducing the risk of damage when handling. Ideally, it should only be necessary to try on a simple garment three times. More complex styles may need more fittings but your aim should always be to achieve a successful display with the fewest possible fittings.
When applying wadding to a display form it needs to be securely stitched to maintain the desired body profile throughout the duration of the exhibition. The techniques explained in this chapter are intended for use with museum displays at a single venue. If the exhibition is to travel to other venues, then additional stitching to the wadding or more rigid petticoats may be needed to prevent movement during transportation. Travelling exhibitions have complex needs and should always be discussed with professional technicians and art movers experienced with this work.
NOTES
1. Off-gassing refers to the practice of allowing a period of time for harmful chemicals used in the production of mannequins and bust forms to evaporate in a wellventilated space.
2. A range of Proportion bust forms and mannequins are produced by Kesslers London Ltd and are available from https://proportionlondon.com
3. Washed in water as hot as the manufacturer’s instructions will allow to remove any applied fabric finish but without detergent. For cotton jersey this would be 90º C.
4. See Appendix for a sample garment measuring chart and padding diagram.
5. The smaller the number the thicker the thread. A 40wt thread will be thicker than a 120wt because it is denser. Usually this is abbreviated to 30 or 120 thread.
6. The name and instructions for special stitches to stitch jersey fabrics will depend on the brand of sewing machine used but the sewing machine manual will give clear instructions for how to use the relevant stitch.
7. Balance marks are used in pattern making to help align pattern pieces when making garments.
8. Silk habotai is a fine plain weave silk often used as a lining in couture garments. It is available in light, medium and heavy weights.