Stitching
The most common stitch used when applying polyester wadding is ‘herringbone stitch’ (see figure 6.8). It is used to attach layers of wadding to the form and to sculpt them into the desired shape. A curved needle is used for his purpose (see figure 6.9b).
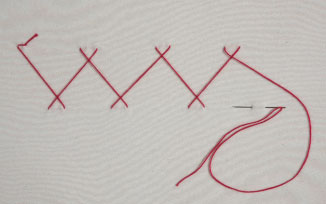
Figure 6.8 Herringbone stitch. © Author. Photography Peter Greenland.

Figure 6.9a Herringbone stitch used to attach wadding to extend the back of the hips into a support for a bustle. © Author. Photography Peter Greenland.
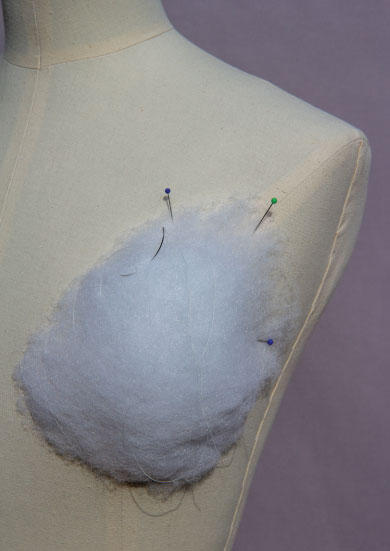
Figure 6.9b Using a curved needle and herringbone stitch to attach wadding to increase the bust size. © Author. Photography Robbie Pettigrew.
Needles
The curved needles used to apply wadding (see figure 6.6 1) can be purchased in many sizes from thick needles used in upholstery to delicate medical needles used for eye surgery. Collecting a range of sizes is a good idea. Generally, a fine, medium to large, curved surgery needle is the easiest to use when stitching wadding. Larger upholstery needles can also be useful if thick adhesive has been used to attach the final cover to the bust form. However, as a result of their thickness, they can make holes in the calico covering the form, so use with caution. In some cases, a thicker stronger needle may be the only option as more delicate needles can snap under the tension needed to stitch through the adhesive. Inserting any needle into a fabric to which adhesive has been applied is difficult and a small pair of ‘jewellery pliers’ (see figure 6.6 6) can be helpful when pulling the needle through the fabric. It is important that the foundation layers of wadding are very tightly stitched and using a curved needle is an essential technique to develop for this purpose.
Using a measurement chart and a padding diagram
Throughout this book, the principal aim is to minimize the number of times a garment needs to be tried on a mannequin or bust form to check its fit. The importance of taking accurate measurements from a garment and using a measurement chart has been discussed in Chapter 5.
Using a simple ‘padding diagram’ to show where wadding needs to be added to customize the display form alongside a measurement chart will ensure that nothing is missed (see figure 6.10a and b). By comparing the garment measurements on the chart with their corresponding areas on the mannequin or bust form, any areas needing to be redefined will be clearly visible. Drawing the additional padding on the diagram creates an image of the final shape that will be required (see figure 6.11b).4
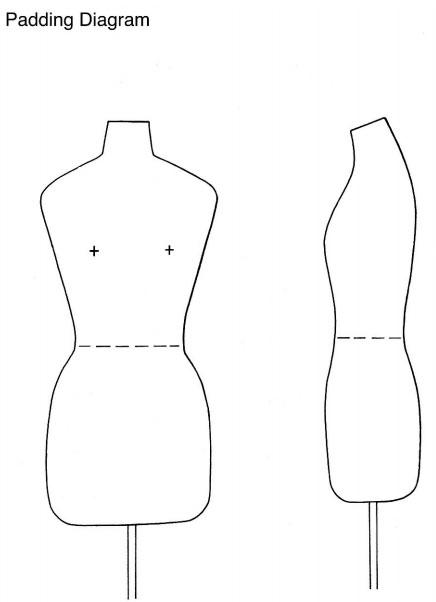
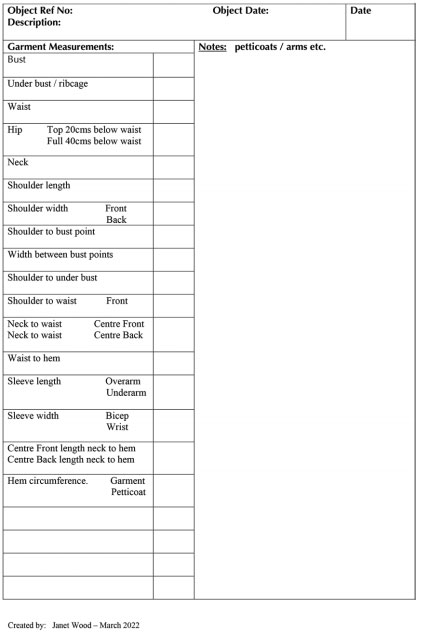
Figure 6.10a and b Examples of a basic ‘Padding Diagram’ and ‘Measurement Chart’. © Author.
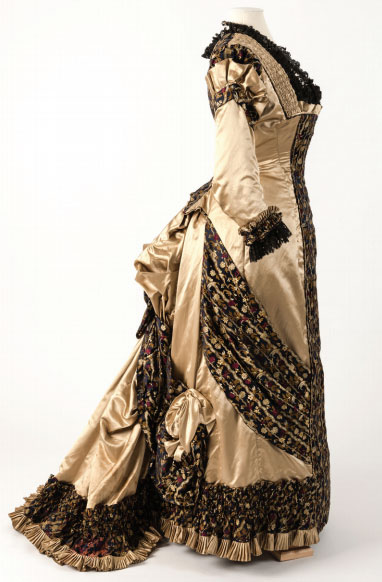
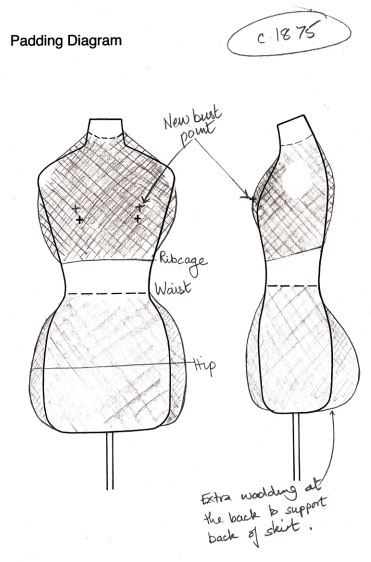
Figure 6.11a and b An example of how a padding chart can be used for the dress from c.1875. The shaded areas on the sketch show where padding needs to be applied to adapt the shape of the bust form. © Sketch Author. © Dress, Fashion Museum Bath.
Step-by-step process for customizing a bust form
Having completed a full analysis of the construction of your garment and established its vulnerable areas, the process of customizing the chosen display form can begin. The following method has been developed for working with bust forms, but also works for mannequins with the addition of a tight base cover as previously described.
MARK THE BUST POINT AND WAISTLINE
Using the garment measurements on the measurements chart and information noted on the padding diagram, compare the bust point and waistline positions of the garment with the bust point and waistline positions on the bust form. Correctly locating these reference points on the form is the key to a successful display, so take time to be accurate.
Figure 6.12 shows the original position of the bust and waist on the bust form marked with black thread and glass-headed pins. The new, higher and widened bust point and waistline positions of the garment are shown marked in red (see figure 6.13).
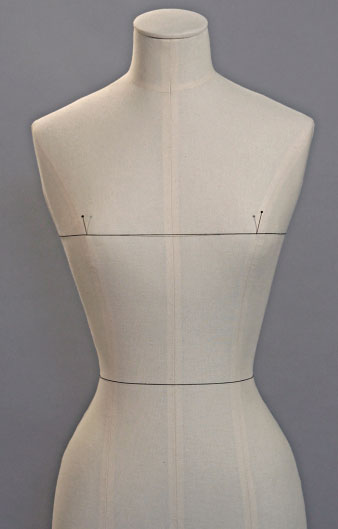
Figure 6.12 Bust form showing the bustline and waistline marked with black threads. © Author.
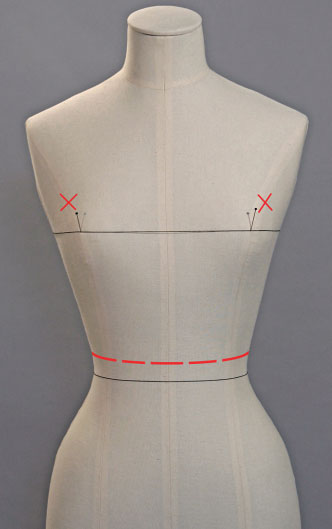
Figure 6.13 Bust form showing the bust points of the garment marked with red crosses and the waistline marked with the dashed red line. © Author.
RE-POSITIONING THE BUST POINT AND INCREASING THE BUST SIZE
Crossed glass-headed pins are used to mark the new bust point on the bust form and another glass-headed pin marks the new waist position. Using the crossed pins as the reference for the new bust point, remove the pins and replace with a small circle of polyester wadding and stitch to the bust form using herringbone stitch (see figure 6.14).
Build up layers of wadding, starting with a small circle and increasing the size with each layer (see figure 6.15). Each circle is stitched in place using herringbone stitches. The first layers, next to the bust form, are stitched securely to the form with tight stitches and strong dressmaking thread, 30wt or 40wt. A&E Gütermann™ have a strong polyester thread, M 782, which works well for applying the base layers of wadding. Subsequent layers are stitched with finer thread and less tension, 50wt to 120wt.5 Standard polyester or cotton sewing thread used for dressmaking is fine in the weights mentioned. Stitches are pulled tight enough to securely hold the wadding in place but without creating a ‘quilted’ effect. After the wadding has been applied, adding more herringbone stitching and pulling the thread slightly tighter can make subtle adjustments to the bust profile.
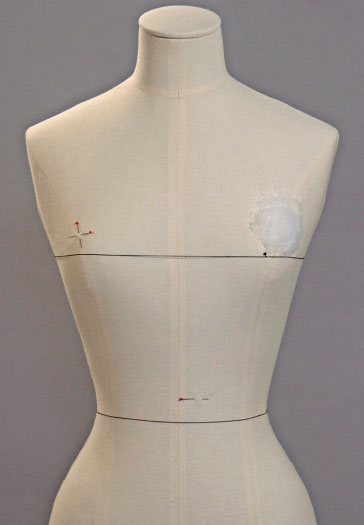
Figure 6.14 A small circle of wadding replaces the crossed pins marking the new bust point. © Author. Photography Robbie Pettigrew
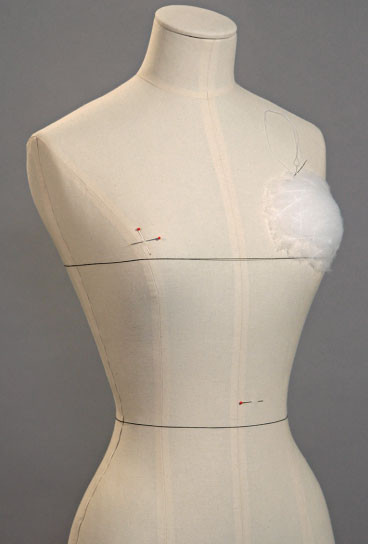
Figure 6.15 More circles increasing in size are added until the required bust measurement is achieved. © Author.